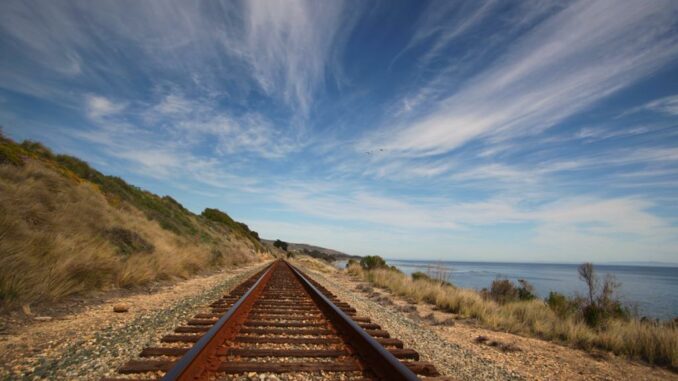
Railroad ballast is a crucial component of the rail transportation system. It is a crushed stone or gravel material that is used to support and level the tracks in a railroad track bed. The primary purpose of ballast is to provide stability to the tracks, allowing trains to run smoothly and safely. Additionally, it helps to drain water and other materials away from the tracks. Without proper ballast, tracks can become unstable and unsafe for trains to operate on.
The size and composition of ballast can vary depending on the type of train and the conditions of the track bed. For example, heavy freight trains require a stronger and more durable ballast than lighter passenger trains. In areas with heavy rainfall or snowfall, a ballast with good drainage properties is necessary to prevent water from accumulating on the tracks. Similarly, in regions with extreme temperatures, a ballast that can withstand the heat and cold is needed.
Traditionally, railroad ballast has been made of crushed stone, such as granite or limestone. These materials are hard and durable, making them well-suited for use as ballast. However, in recent years, other materials such as recycled concrete and slag have been used as well. These materials are often more cost-effective than traditional crushed stone and can also be more environmentally friendly.
The process of laying ballast begins with the removal of the old ballast. This is done using specialized equipment such as ballast regulators and tamper machines. The old ballast is loaded onto trucks and transported away for disposal or reuse. Once the old ballast has been removed, the track bed is inspected for any damage or defects that need to be repaired before the new ballast can be laid.
Next, the new ballast is spread evenly across the track bed using specialized equipment such as ballast spreaders. The ballast is spread to a depth of about 10 inches, with the top layer being slightly shallower to allow for proper drainage. Once the ballast has been spread, it is tamped down using a tamper machine. This compacts the ballast and ensures that it is level and stable.
The process of tamping the ballast is very important as it helps to eliminate any voids or air pockets that may have been created during the spreading process. These voids can cause the ballast to shift and become unstable, which can lead to track failure and potential accidents. Proper tamping also helps to ensure that the ballast is in close contact with the subgrade, which helps to transfer the load of the train to the ground.
After the ballast has been tamped, the track is inspected again to ensure that it is level and stable. Any adjustments that need to be made are done at this stage. Once the track has been deemed safe, trains can begin running on it again.
The process of maintaining ballast is an ongoing one, as ballast can become worn or degraded over time. Regular inspections are conducted to check for any issues that may arise, such as washouts or settling. If these issues are identified, they are addressed as soon as possible to ensure the continued safety and stability of the tracks.
So, while that ballast may be hard to walk on (why are you walking on train tracks anyway), it makes the trains run smoother and safer.
Be the first to comment